Goodyear's advances in tire simulations are reducing the need for real-world testing
Goodyear's tire simulations cut 60,000 test miles per cycle with advanced modeling.
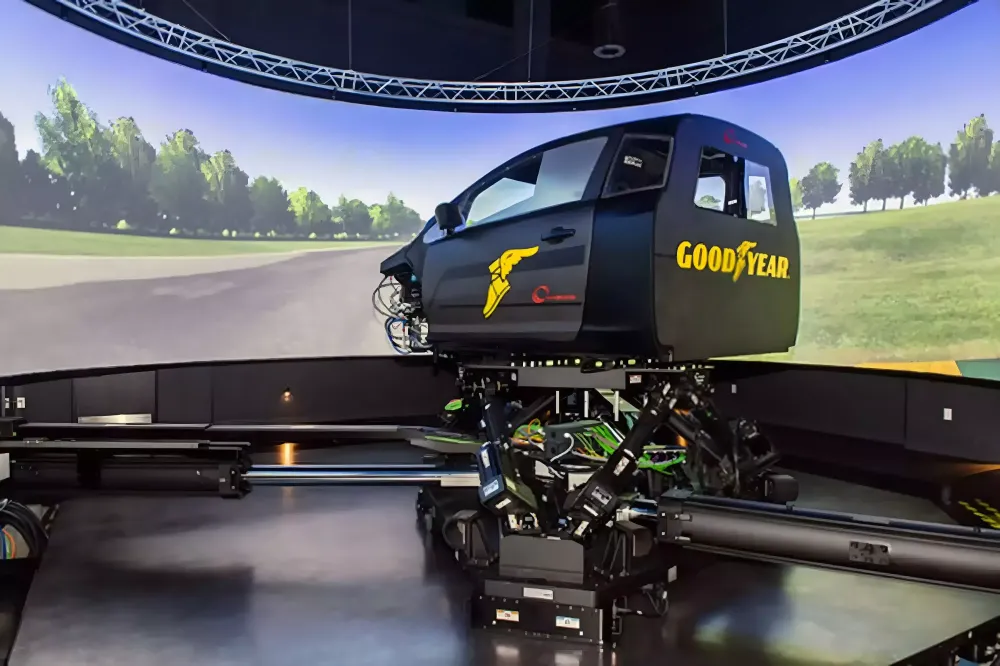
Goodyear's advancements in tire simulations are minimizing the necessity for extensive real-world testing by eliminating the requirement for 60,000 miles of test track driving per development cycle. According to Chris Helsel, Goodyear's Chief Technology Officer, the progress involves overcoming challenges related to simulating tire deformation, tire-road contact, and intricate tread patterns using methods like finite element analysis.
Enhanced tire simulation capabilities have evolved over time from basic contact patch predictions to high-fidelity modeling in diverse weather conditions. The introduction of dynamic driver-in-the-loop simulators in Akron, Ohio, and Luxembourg allows for efficient tire testing without physical prototypes, resembling systems used in motorsports.
These innovations have considerably accelerated the tire development process. Steve Rohweder, Goodyear's VP of Technology Development, observes that high-fidelity models have reduced the need for multiple physical iterations to just one build and confirmation, cutting the requirement for approximately 13,000 tires and saving resources in each development cycle.