How 3D printing is changing the way NASCAR builds cars
3D printing innovates NASCAR car production, enhancing performance and reducing costs.
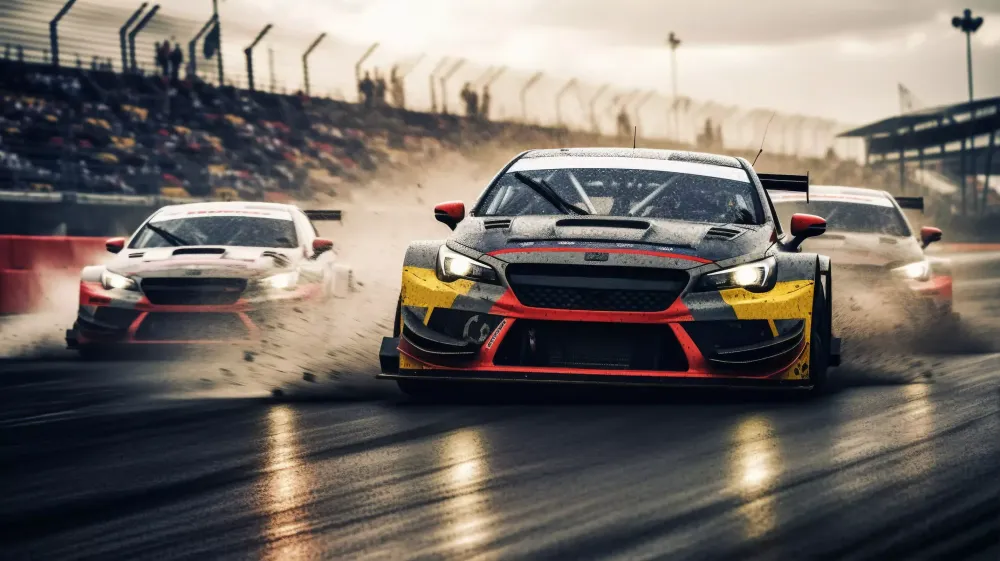
NASCAR is transforming its approach to car development by integrating 3D printing technology, advancing customization, and efficiency. In collaboration with Stratasys, the official 3D Printing Partner of NASCAR, the sport now benefits from innovative materials like ULTEM 9085 and plant-based Nylon11, which cater to the extreme conditions on the racing track.
The application of 3D printing methods such as Fused Deposition Modeling (FDM) and Stereolithography (SLA) has enabled teams to produce intricate geometries and precise parts rapidly. These advancements offer NASCAR a competitive edge by reducing lead times and production costs, paving the way for more intricate aerodynamic components used during wind tunnel testing.
A notable development includes Joe Gibbs Racing utilizing this technology to address issues with ill-fitting components efficiently, saving crucial time. Looking forward, the industry is expected to focus on increasing the throughput of 3D printing systems, a move that will further capitalize on these efficiency gains. Additionally, the technology is extending beyond racing circuits, with custom car modifications receiving significant attention at showcases like SEMA.